两化融合/智能制造
当前,我国钢铁产业面临产能过剩、需求低迷、国家供给侧改革战略的迫切性,需要加强提质增效、节能减排。而我国钢铁企业生产管理发展趋势是个性化、定制化、多品种、小批量,关键要协调产销矛盾,以降低生产、库存、物流成本。为此,我国钢铁行业需要打造面向制造业的“互联网+”产业生产体系,推动产业融合,力促钢铁转型升级,因而构建钢铁全流程智能制造系统非常迫切,市场前景广阔。
亚仿钢铁企业智能制造解决方案的智能化特征主要表现在:
(1) 建立企业大数据管理平台,实现企业数据信息化、知识化和资产化,成为企业的财富和知识源泉;
(2) 建立中央管控中心,使企业管理模式逐步扁平化;
(3) 基于工业大数据系统实现企业全流程信息的实时、共享和一体化,解决数据传输的滞后性,实现各生产环节的信息实时共享和最优化衔接,保证工艺和装备生产效率最高,产品质量最佳,并适应多品种小批量的生产模式;
(4) 建立工序成本计算模型和利润预测模型,为生产和采购决策提供支持;
(5) 建立能源系统仿真模型和仿真试验床,实现能源系统的均衡、高效利用,可有效提升能源系统的平衡预测和优化调度能力,以确保能源稳定供给和生产安全运行,同时最大效率利用二次能源;
(6) 对生产过程中的关键设备进行统一的监控,当设备出现故障时能够进行报警,并且对所影响的设备和区域进行联动报警;
(7) 实现了质量数据在上下游工序的实时共享和质量问题的全流程追溯;
(8) 实现了对安全生产、环保系统的集中监测系统,实现物耗、能耗和污染物排放最低化的绿色生产;
(9) 建立电子化的审批流程和移动办公支持系统,打通各部门之间的信息链路,实现高效的联合工作,提高办公效率;
(10) 建立网络化的培训与考核系统,打造学习型企业,为公司的经营和发展提供有力的支援和保障;
(11) 项目核心技术“仿真控制信息三位一体平台” 是实现两化融合的基础性平台,是拥有完全自主知识产权的国产工业化软件平台,完全符合国家自主创新战略,对促进两化融合、提高创新能力具有重要意义;
(12) 本项目在结构上突破了钢铁行业传统的五层信息化架构,以建立数据为中心,实现企业生产运营过程的数字化、模型化、可视化、网络化、智能化,为钢铁企业实施两化深度融合、实现跨越式发展闯出来一条全新的技术路线。
产品及解决方案
-
●生产监控与综合调度中心
生产监控与综合调度中心平台使企业管理模式逐步扁平化,可以增强全厂信息的透明度,加强生产管理者对全厂生产情况的管控力度,为生产管理者的高质量高效率决策提供信息支持。
-
●数字化巡检系统
数字化巡检系统包括手持巡检仪、服务器、管理软件系统等,突破了传统人工巡检的诸多局限,对于提升巡检质量、保障设备安全运转、提升设备管理水平有非常重要的作用。
-
●设备维护智能化系统
设备维护智能化管理系统通过建立设备全生命周期静动态信息的设备“活台账”,构建 “设备实时监控”+“设备状态分析”+“设备点检定修”相结合的设备维护智能化管理平台,极大地提升了设备管理的透明度,提高了管理效率,消除了缺陷隐患,是向智能制造模式转型和提升的核心基础。
-
●综合指标分析系统
企业综合指标分析系统是建立一个企业统一的数据中心,以指标形式,将沉淀在各个业务系统数据库中的基础数据调动起来,对数据进行适当的抽取、提炼、整理和组织,形成进一步分析决策的基础。系统采取以指标体系为牛鼻子,层层倒推,找到数据源头;指标数据尽可能自动获取,人工输入只作为补充手段。系统提供灵活、方便的查询分析手段;提供自定义报表功能,支持多种格式的报表模版,可方便生成各种报表。
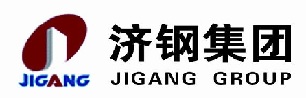